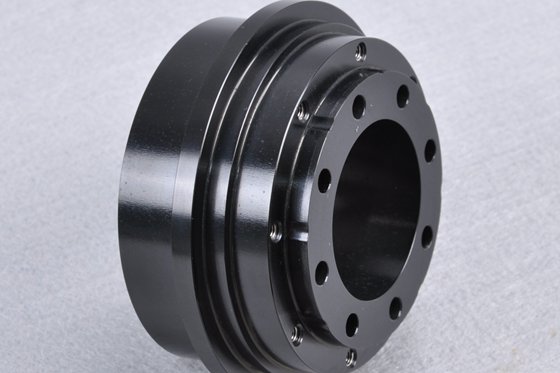
Certainly! Here’s a comprehensive guide to black oxidation treatment coating for metal:
What is Black Oxide Coating?
Black oxide coating, also known as blackening, is a conversion coating for ferrous materials (mostly steel and iron) where the surface of the metal is chemically converted to black iron oxide. This process provides several benefits, including corrosion resistance, improved appearance, and increased wear resistance.
The Black Oxide Process:
- Cleaning: The metal surface must be thoroughly cleaned to remove any contaminants, oils, or rust. This is usually done through a combination of cleaning methods such as alkaline cleaning, acid cleaning, and abrasive cleaning.
- Activation: After cleaning, the metal is immersed in an activating solution to prepare the surface for the black oxide reaction.
- Black Oxide Bath: The metal is then immersed in a hot black oxide bath, typically consisting of sodium hydroxide, nitrites, and other proprietary chemicals. This bath initiates a chemical reaction with the surface of the metal, forming a layer of black iron oxide.
- Rinsing: The metal is thoroughly rinsed to remove any residual chemicals from the black oxide bath.
- Sealing (Optional): In some cases, a sealing process may follow to enhance corrosion resistance and further improve the appearance of the black oxide coating.
Advantages of Black Oxide Coating:
- Corrosion Resistance: Black oxide coating provides a protective layer that helps prevent corrosion and rust on the metal surface.
- Appearance: The black finish is aesthetically pleasing and can be used for decorative purposes.
- Durability: The black oxide layer improves wear resistance and can contribute to the overall durability of the metal.
- Cost-Effective: Compared to some other coating methods, black oxide coating is often a cost-effective option.
Applications:
- Firearm Components: Black oxide coating is commonly used on firearm components for both functional and aesthetic reasons.
- Automotive Parts: Various automotive parts, such as fasteners and brackets, can benefit from black oxide coating.
- Tools and Hardware: Hand tools and hardware items often undergo black oxide coating for improved durability.
- Industrial Equipment: Certain industrial equipment and machinery components may be treated with black oxide for corrosion resistance.
Considerations:
- Material Compatibility: Black oxide coating is primarily used on ferrous materials. It may not be suitable for non-ferrous metals like aluminum or copper.
- Thickness Control: The thickness of the black oxide layer can be controlled to some extent, but it’s generally a thin coating.
- Post-Coating Treatments: Depending on the application, additional treatments like oiling or waxing may be applied to enhance performance.
Safety Precautions:
- Chemical Handling: The chemicals used in the black oxidation process can be hazardous. Proper safety measures, including personal protective equipment (PPE), should be followed.
- Ventilation: Adequate ventilation is essential in areas where black oxide coating is applied to ensure the safe dispersal of fumes.
Conclusion:
Black oxide coating is a versatile and widely used process that provides numerous benefits to metal surfaces. Understanding the process, its applications, and safety considerations is crucial for achieving optimal results. If you’re considering black oxide coating for a specific application, it’s advisable to consult with professionals or experts in the field for guidance tailored to your needs.